Discover my Amazing
Research Space!
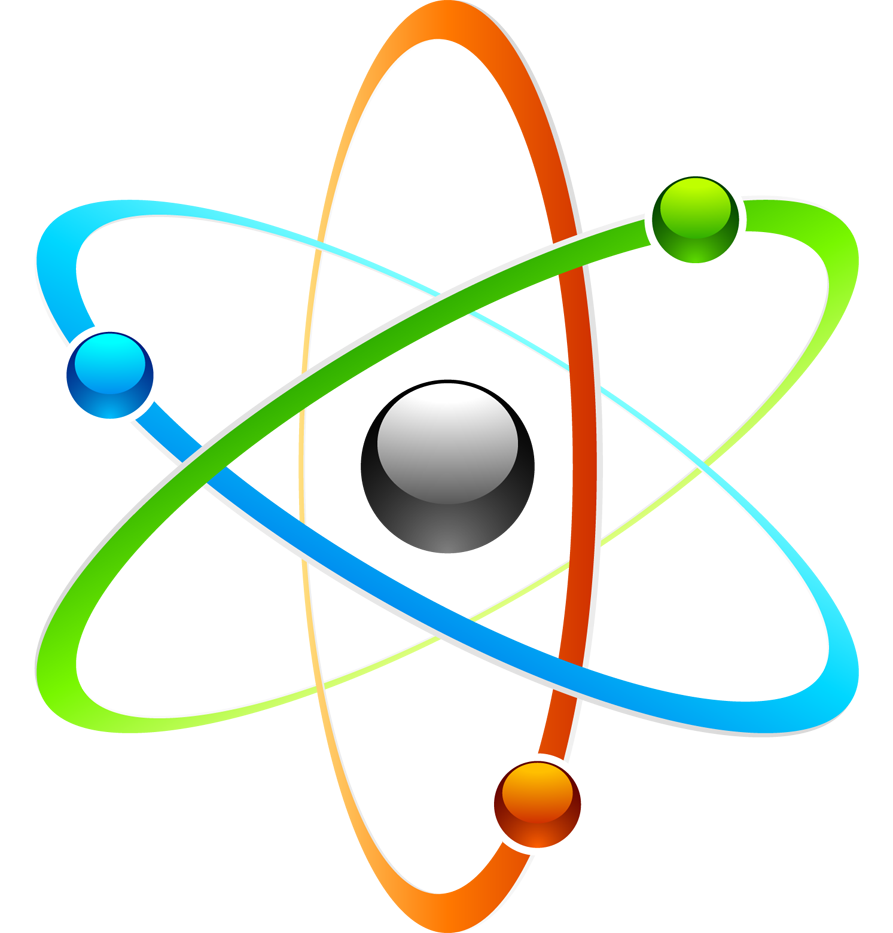
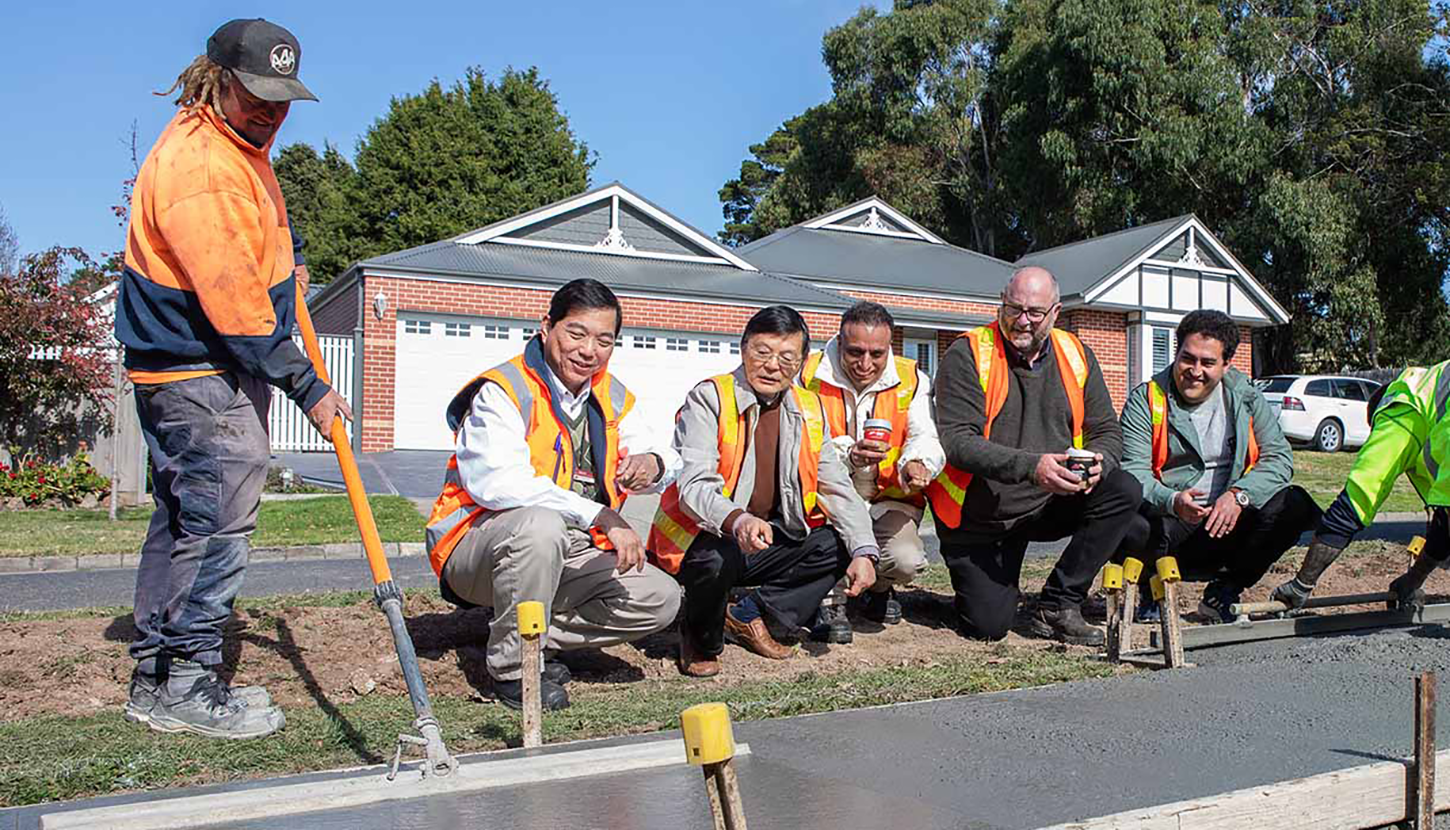
Picture Credit: Carelle Mulawa-Richards, RMIT University
Blog 6: From the Lab to the Sidewalk: The World's First Coffee Concrete Footpath
Last updated: May 23, 2024 06:30 PM AEST
In a groundbreaking collaboration between RMIT University and Macedon Ranges Shire Council, the world's first coffee concrete footpath has been laid, marking a significant milestone in the quest for sustainable construction practices.
The Power of Coffee Waste
Coffee is one of the most popular beverages worldwide, with millions of cups consumed daily. However, this popularity comes at an environmental cost. In Australia alone, approximately 75 million kilograms of ground coffee waste are generated annually, with the majority ending up in landfills. This figure skyrockets to a staggering 10 billion kilograms of spent coffee grounds each year. As the world becomes increasingly focused on sustainability and waste reduction, researchers have been seeking innovative ways to repurpose these waste materials and mitigate their environmental impact.
From Waste to Resource: The Coffee Biochar Process
The key to unlocking the potential of spent coffee grounds lies in a process called pyrolysis. By heating the grounds to a specific temperature (350°C) in the absence of oxygen, the RMIT researchers discovered that they could create a carbon-rich, porous material known as biochar. When incorporated into concrete at an optimal replacement level of 15% by volume of sand, this coffee-derived biochar increased the compressive strength of the concrete by an impressive ~30%. The porous nature of the biochar allows it to absorb water and contribute to the internal curing of the concrete, leading to enhanced strength development.
Putting Research into Practice: The Gisborne Footpath Trial
To put their research findings into practice, the RMIT team partnered with Macedon Ranges Shire Council to conduct a world-first coffee concrete footpath trial in Gisborne, Victoria. The trial involved incorporating coffee and wood-chip biochar into two separate concrete footpaths, replacing a portion of the river sand traditionally used in the mixture. Shane Walden, the Council's Director of Assets and Operations, expressed his excitement about the project, stating that residents won't notice any difference in the appearance or smell of the concrete, but the benefits to the environment and the community are significant.
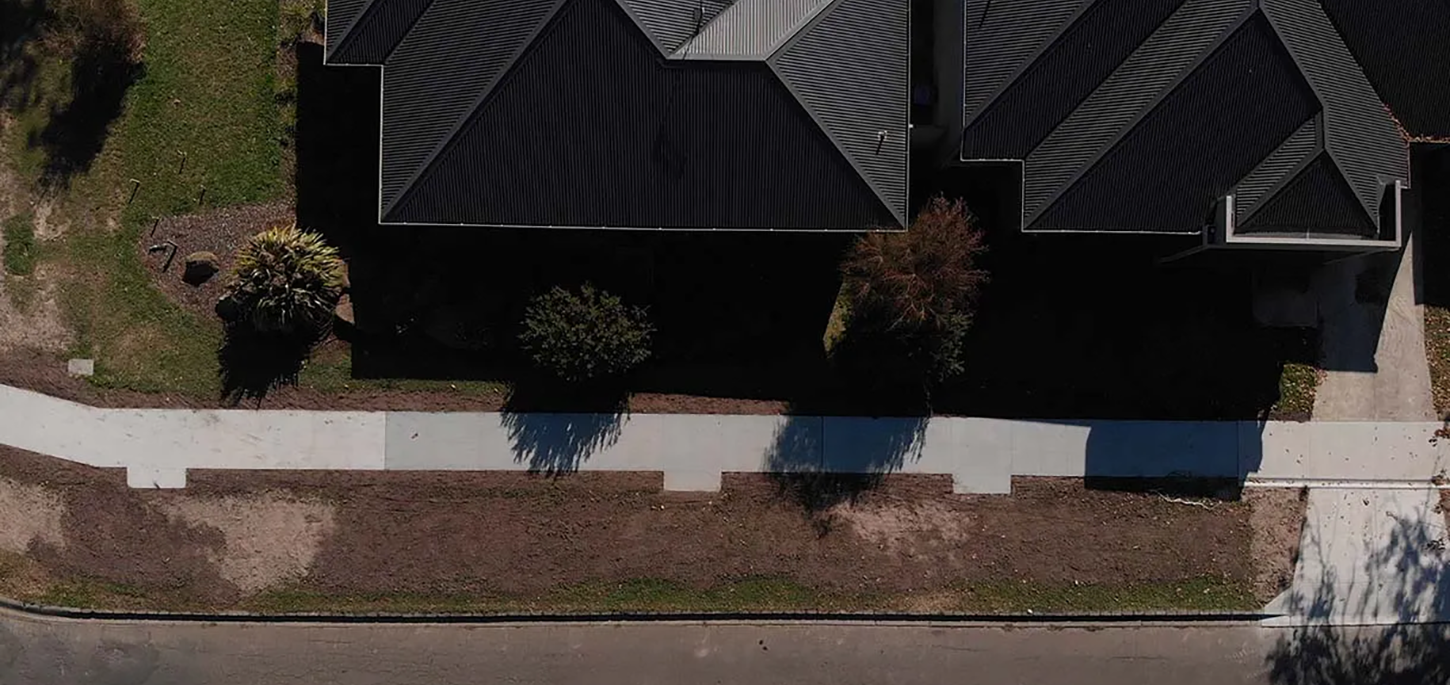
Aerial view of the finished footpath in Gisborne. Picture Credit: Chris Matthews, Macedon Ranges Shire Council
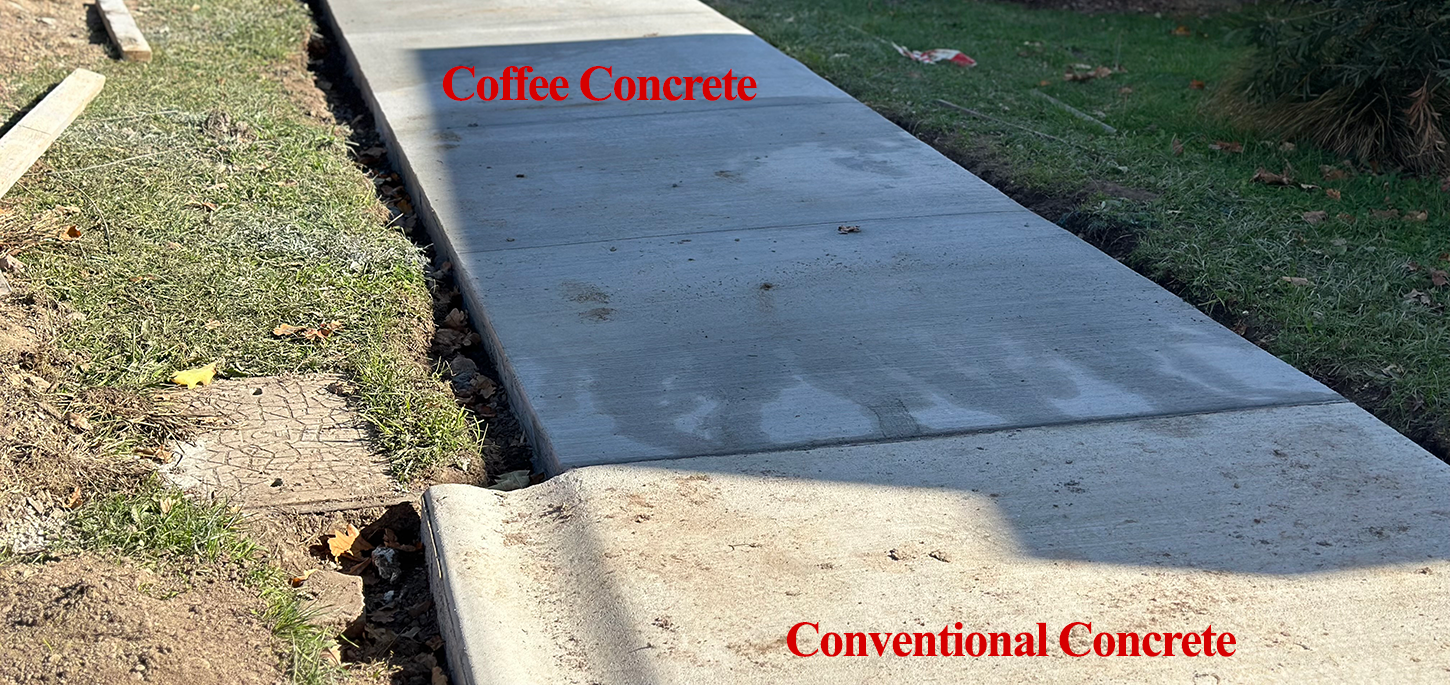
Close-up view of the finished footpath in Gisborne. Picture Credit: Jeetendra Kathayat, Macedon Ranges Shire Council
The Future of Coffee Concrete
Building upon the success of the Gisborne footpath trial, the RMIT team is now collaborating with BildGroup, an Australian-owned civil infrastructure, asphalt paving, and road profiling company, to deliver several upcoming coffee biochar concrete projects across Victoria. These projects aim to further validate the real-world performance and scalability of this innovative solution. By partnering with BildGroup, the researchers will have the opportunity to monitor the long-term durability and environmental benefits of coffee biochar concrete in various infrastructure applications. The collaboration between academia and industry is crucial in bridging the gap between laboratory research and practical implementation, paving the way for the wider adoption of sustainable construction practices. As more projects incorporating coffee biochar concrete are rolled out, the potential for this technology to revolutionize the construction industry and contribute to a greener future becomes increasingly evident.
Potential Benefits and Cost Savings
The incorporation of coffee biochar into concrete offers a range of potential benefits and cost savings for the construction industry. By achieving a 30% increase in concrete strength, the required cement content could potentially be reduced by as much as 10%, according to Dr Roychand. This reduction in cement usage, combined with the diversion of waste from landfills, promotes sustainability and supports the development of a circular economy.
List of Benefits
- Enhanced compressive strength: The addition of coffee biochar, particularly at a 15% replacement level of sand, can increase the compressive strength of concrete by up to ~30%.
- Potential for cement reduction: The significant increase in concrete strength due to coffee biochar incorporation could allow for a reduction in the required cement content, leading to lower environmental impact and cost savings.
- Waste utilization: By using spent coffee grounds to produce biochar for concrete applications, this waste material is diverted from landfills, promoting sustainability and a circular economy.
- Improved microstructure: Coffee biochar exhibits excellent bonding with the cement matrix, and the cement paste penetrates the porous biochar material, contributing to enhanced strength development.
- Internal curing: The porous nature of coffee biochar allows it to absorb and retain water, which is released as the internal relative humidity of the cement matrix drops, providing internal curing and further enhancing strength development.
- Reduced environmental impact: Incorporating coffee biochar in concrete can help reduce the carbon footprint of the construction industry by minimizing waste, reducing cement usage, and sequestering carbon within the concrete.
- Potential for large-scale application: The research suggests that 100% of the waste spent coffee grounds produced in Australia could be consumed by the construction industry if used as a replacement for fine aggregates in concrete.
- Improved sustainability: The use of coffee biochar in concrete aligns with the goals of sustainable construction practices and contributes to the development of eco-friendly building materials.
Research Team
Rajeev Roychand, Shannon Kilmartin-Lynch, Mohammad Saberian, Jie Li
Publication Reference
Transforming spent coffee grounds into a valuable resource for the enhancement of concrete strength is published in the Journal of Cleaner Production (DOI: 10.1016/j.jclepro.2023.138205)
Carbon sequestration from waste and carbon dioxide mineralisation in concrete – A stronger, sustainable and eco-friendly solution to support circular economy is published in the Journal of Construction and Building Materials (DOI: 10.1016/j.conbuildmat.2023.131221)
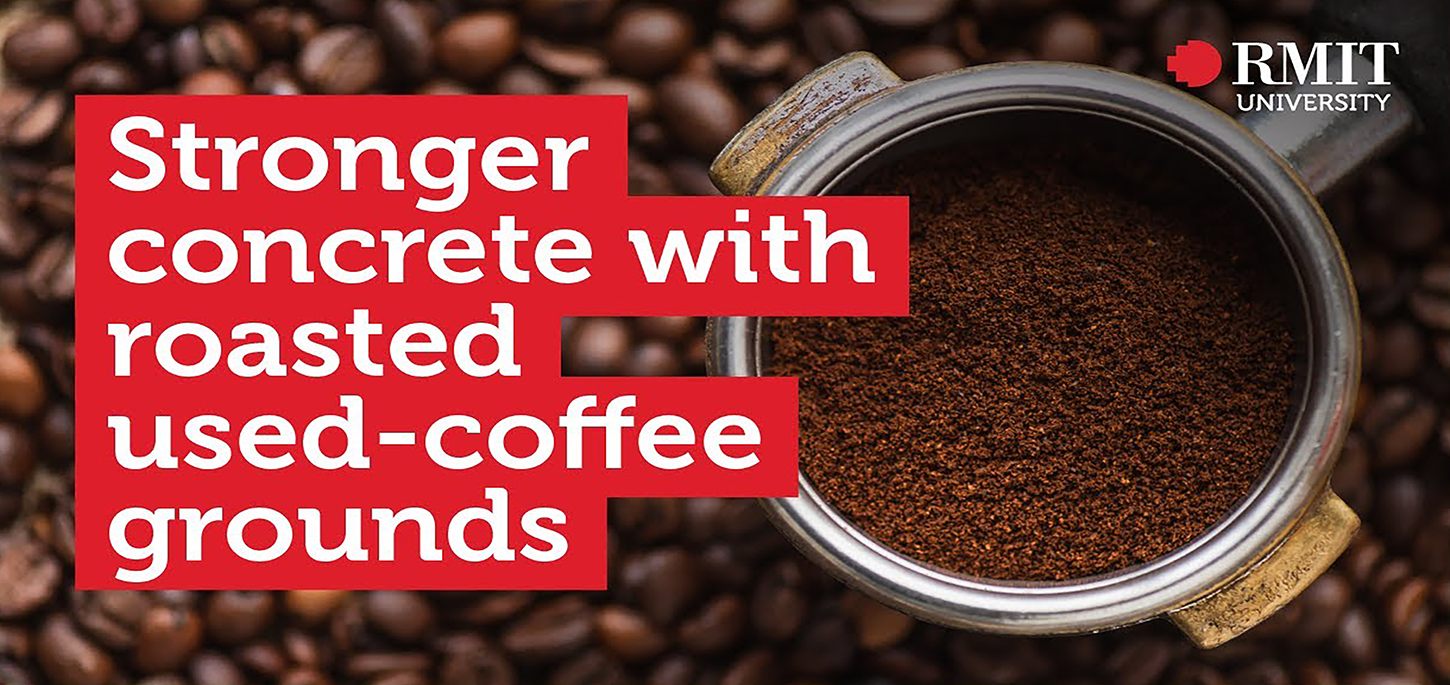
Blog 5: From Lattes to Concrete: The Surprising Strength of Coffee Waste
Imagine sipping your morning latte and knowing that the spent coffee grounds from your cup could one day form the foundation of your home. This idea may soon become a reality, thanks to a groundbreaking study by engineers at RMIT University in Melbourne, Australia.
Motivation Behind this Innovation
The driving force behind this groundbreaking study was the alarming amount of organic waste ending up in landfills, contributing significantly to greenhouse gas emissions. In Australia, approximately 6.87 million tonnes of organic waste are dumped in landfills annually, accounting for 3% of the country's total greenhouse gas emissions. Recognizing the urgent need to address this issue, the research team at RMIT University decided to shift their focus towards developing innovative solutions that could divert this waste from landfills and transform it into a valuable resource. Interestingly, the idea to start with coffee grounds emerged during a team meeting over a cup of coffee, highlighting the serendipitous nature of scientific discovery.
The Coffee Waste
Coffee is one of the most widely consumed beverages in the world, with millions of cups enjoyed daily. However, this popularity comes at a significant environmental cost. In Australia alone, around 75,000 tonnes of spent coffee grounds end up in landfills each year, contributing to a growing waste problem. Globally, this number skyrockets to a staggering 10 billion kilograms of coffee waste annually. As the world becomes increasingly focused on sustainability and waste reduction, researchers are constantly seeking innovative ways to repurpose these waste materials and mitigate their environmental impact.
From Coffee Waste to Biochar
Coffee is one of the most widely consumed beverages in the world, with millions of cups enjoyed daily. However, this popularity comes at a significant environmental cost. In Australia alone, around 75,000 tonnes of spent coffee grounds end up in landfills each year, contributing to a growing waste problem. Globally, this number skyrockets to a staggering 10 billion kilograms of coffee waste annually. As the world becomes increasingly focused on sustainability and waste reduction, researchers are constantly seeking innovative ways to repurpose these waste materials and mitigate their environmental impact.
Coffee Biochar for a Stronger Concrete
When incorporated into concrete, the coffee-derived biochar proved to have remarkable effects. At an optimal replacement level of 15% by volume of sand, the biochar increased the compressive strength of the concrete by an impressive 29.3%. The porous nature of the biochar allows it to absorb water and contribute to the internal curing of the concrete, leading to enhanced strength development.
The Role of Pyrolysis Temperature
The researchers found that the temperature at which the biochar is produced plays a crucial role in its effectiveness. Biochar created at 350°C provided the best results, while that produced at 500°C showed a decrease in strength due to its more fragile structure. This highlights the importance of fine-tuning the pyrolysis process to maximize the benefits of the biochar.
Environmental and Economic Benefits
- ~30% increase in concrete strength
- This significant increase in strength can be leveraged to reduce the required cement content
- Creates a potential for the 100% uptake of this waste material for concrete applications
- This waste to resource transformation creates a potential for diverting this waste from going to landfills, promoting sustainability, and closed loop circular economy.
Research Team
Rajeev Roychand, Shannon Kilmartin-Lynch, Mohammad Saberian, Jie Li, Guomin Zhang, Chun Qing Li
Publication Reference
Transforming spent coffee grounds into a valuable resource for the enhancement of concrete strength is published in the Journal of Cleaner Production (DOI: 10.1016/j.jclepro.2023.138205)
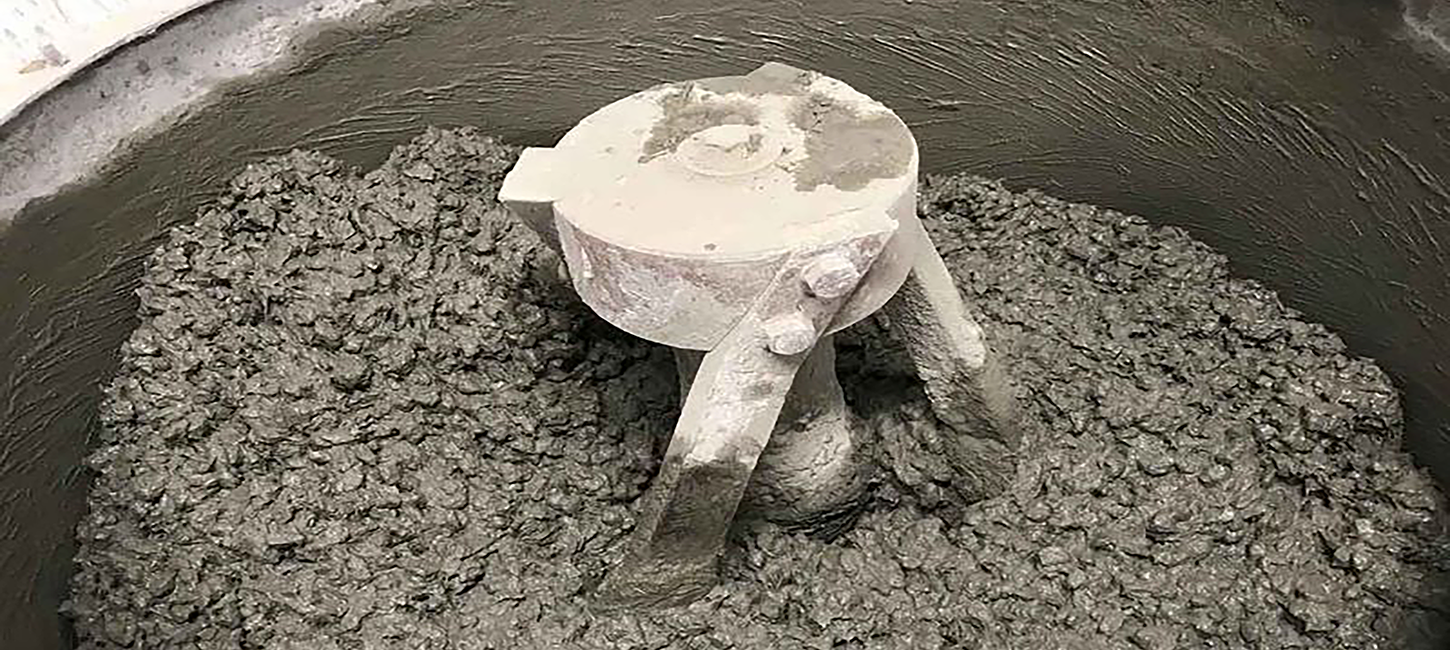
Blog 4: Rubber Meets the Road: Transforming Tires into Sustainable Concrete
In a world where sustainability is no longer a choice but a necessity, engineers have achieved the remarkable feat of creating concrete that completely replaces conventional aggregates, such as gravel and crushed rock, with rubber derived from discarded tires.
A Pressing Issue
Every year, billions of waste tires end up in landfills, posing significant environmental challenges. These non-biodegradable materials not only occupy valuable land space but also contribute to air and water pollution when burned or stockpiled. The need for effective recycling methods has never been more urgent.
From Waste to Resource
Enter the visionary team of researchers from RMIT University in Melbourne, Australia. Led by Dr. Mohammad Momeen Ul Islam, they have developed an ingenious method that transforms waste tire rubber into a valuable resource for the construction industry.
Their innovative approach involves replacing conventional coarse aggregates in concrete entirely with rubber particles from end-of-life tires. By employing a novel compression casting technique, they have successfully created structural lightweight concrete with remarkable mechanical properties.
Strength and Sustainability
The rubber concrete developed by the RMIT team boasts a compressive strength of up to 97% higher than traditional rubberized concrete. This significant improvement in strength is achieved through the compression casting process, which minimizes the gaps between the rubber particles and the cement matrix, resulting in a denser and more durable material.
Moreover, the carbon footprint of this rubber concrete is substantially lower compared to conventional concrete. By utilizing waste tires, which would otherwise end up in landfills, the researchers have found a way to reduce the environmental impact of construction while also conserving natural resources.
A Greener Future
The potential applications of this rubber concrete are vast, ranging from residential construction to infrastructure projects. Its lightweight nature and impressive strength make it an attractive option for builders seeking sustainable alternatives to traditional concrete.
As the world grapples with the urgent need to combat climate change and reduce waste, innovations like rubber concrete offer a glimmer of hope. By turning waste into a valuable resource, we can pave the way to a greener, more sustainable future.
The research conducted by Dr. Islam, Dr. Li, and their team at RMIT University is a testament to the power of scientific ingenuity in addressing global challenges. As more industries embrace such eco-friendly solutions, we can look forward to a world where sustainability is not just a buzzword but a way of life.
Research Team
Mohammad Momeen Ul Islam, Jie Li, Yu-Fei Wu, Rajeev Roychand, Mohammad Saberian
Publication Reference
Design and strength optimization method for the production of structural lightweight concrete: An experimental investigation for the complete replacement of conventional coarse aggregates by waste rubber particles is published in the Journal of Resources, Conservation and Recycling (DOI: 10.1016/j.resconrec.2022.106390)
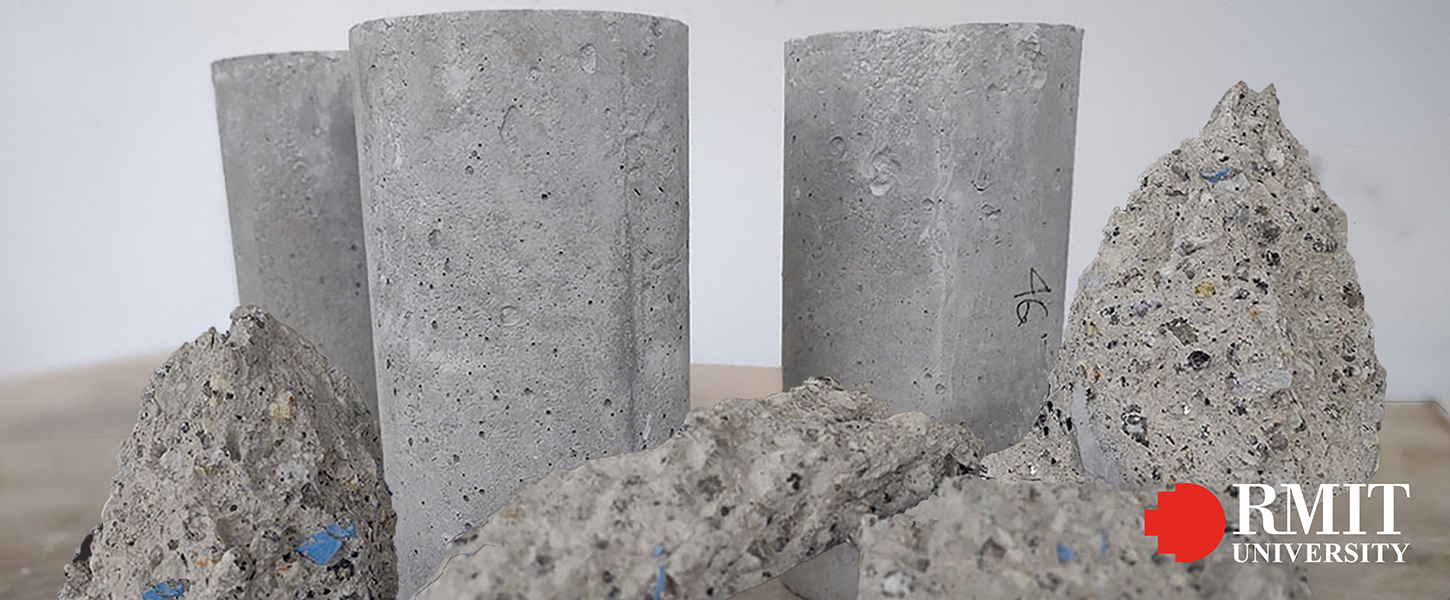
Blog 3: Disposable PPE waste makes concrete stronger by up to 22%
Researchers at RMIT University have found a way to give new life to disposable personal protective equipment (PPE) waste by using it to strengthen concrete, offering a creative solution to the challenge of managing the surge of pandemic-related plastic waste.
The environmental impact of PPE waste
The COVID-19 pandemic has not only strained healthcare systems worldwide but has also created a new stream of plastic waste in the form of discarded PPE. Globally, it is estimated that 129 billion face masks and 65 billion gloves are used each month. This surge in PPE waste has led to increased littering, with discarded items ending up in landfills and oceans, contributing to the growing problem of microplastic pollution.
Recycling PPE waste in concrete
To tackle this environmental challenge, the RMIT research team, led by Dr Shannon Kilmartin-Lynch, has investigated the potential of incorporating shredded PPE waste into structural concrete. By repurposing these materials, they aim to divert waste from landfills and reduce the environmental footprint of the construction industry.
- Nitrile gloves
- Polypropylene face masks
- Isolation gowns
Concrete Strengthening Mechanism
The researchers found that incorporating shredded PPE waste into concrete helps in improving its strength properties. The team attributed these improvements to the strong bond formed between the shredded PPE materials and the cement matrix, as observed through scanning electron microscopy. This strong bond allows for better stress transfer and crack bridging within the concrete mixture.
- Up to 22% higher strength with shredded nitrile gloves
- Up to 17% higher strength with shredded face masks
- Up to 15.5% higher strength with shredded Isolation gowns
Towards a circular economy
The research conducted by the RMIT team demonstrates the potential for a closed loop circular economy approach in the construction industry, where waste materials are repurposed as valuable resources. By incorporating PPE waste into concrete, not only can we reduce the environmental impact of the pandemic but also create a more sustainable built environment.
As the world continues to grapple with the challenges posed by COVID-19, it is crucial to find innovative solutions to manage the waste generated by the pandemic. The work of Dr. Li and his team at RMIT University serves as an inspiring example of how creative thinking and scientific research can help us build a more sustainable future.
Research Team
Shannon Kilmartin-Lynch, Rajeev Roychand, Mohammad Saberian, Jie Li, Guomin Zhang
Publication References
Application of COVID-19 single-use shredded nitrile gloves in structural concrete: Case study from Australia is published in the Journal of Science of The Total Environment (DOI: 10.1016/j.scitotenv.2021.151423)
Preliminary evaluation of the feasibility of using polypropylene fibres from COVID-19 single-use face masks to improve the mechanical properties of concrete is published in the Journal of Cleaner Production (DOI: 10.1016/j.jclepro.2021.126460)
A sustainable approach on the utilisation of COVID-19 plastic based isolation gowns in structural concrete is published in the Journal of Case Studies in Construction Materials (DOI: 10.1016/j.cscm.2022.e01408)
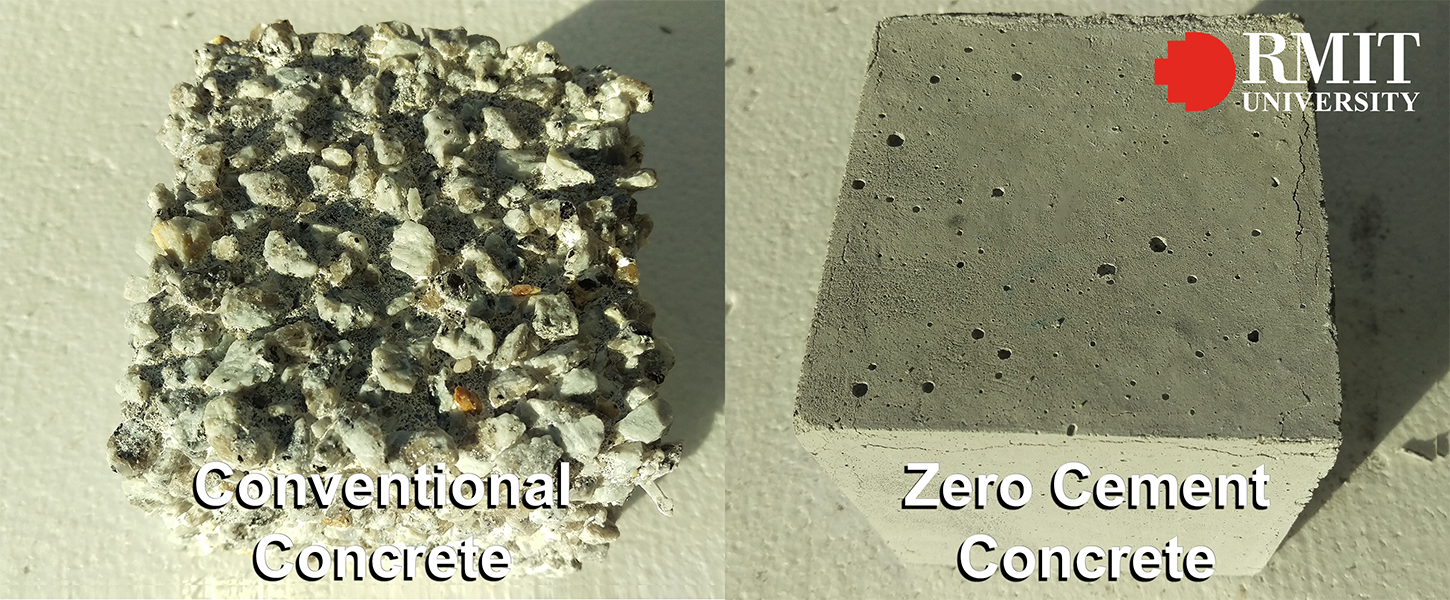
Blog 2: High durability zero cement concrete beats corrosion and resists fatbergs
Researchers from RMIT University have pioneered an innovative zero cement concrete, wielding the power to eliminate corrosion and thwart the formation of fatbergs, thus extending the lifespan of infrastructure like never before.
The problem
Cement concrete, the backbone of our urban infrastructure, not only comes with high carbon footprint, but in the realm of sewage infrastructure, hides a dirty secret. The cement that binds the sand and gravel has a weak link i.e., free lime – a byproduct of cement hydration, that is released into the concrete. In the acidic sewage environment, the concrete rich in free lime becomes a vulnerable target to the corrosive acids, silently corroding the very core of sewage pipes. An even grimmer fate awaits on the inside of the pipes, where the same free lime reacts with fats, oils, and greases (FOGs) in the sewage to form giant, pipe-clogging "fatbergs". Maintaining and upgrading the sewage network comes with high costs and disruptions to the general public. With annual maintenance expenses reaching up to $15 million in Australia, tens of millions in the United Kingdom, and figure skyrocketing to billions in the USA, the financial burden on governments and taxpayers is undeniable.
Deciphering the Code
The team of researchers, led by Dr Rajeev Roychand, have cracked the code, unveiling how free lime, the hidden instigator of concrete corrosion, also plays a pivotal role in the formation of fatbergs. Furthermore, they have demonstrated how this innovative zero cement concrete, free from this inherent vulnerability, can play a crucial role in addressing these challenges.
The Innovation
By harnessing a cocktail of industrial byproducts like fly ash and slag, and fortifying it with nano-silica particles, the researchers have conjured up a concrete capable of withstanding the corrosive conditions inside sewers, while also help in preventing the sewers' worst enemies: corrosion and fatbergs. This innovation has the potential to revolutionize the way we build and maintain our infrastructure.
A sewer pipe dream come true?
While the researchers have shown it's possible to eliminate Portland cement from concrete sewage pipes, the long-term performance of this zero-cement concrete in real-world conditions still needs to be proven. Nevertheless, the study points the way to a future where concrete infrastructure is not only greener, but also lasts longer with less maintenance - a win for sustainability on multiple fronts.
Research Team
Rajeev Roychand, Jie Li, Saman De Silva, Mohammad Saberian, David Law, Biplob Kumar Pramanik
Publication Reference
Development of zero cement composite for the protection of concrete sewage pipes from corrosion and fatbergs is published in the Journal of Resources, Conservation & Recycling (DOI: 10.1016/j.resconrec.2020.105166)
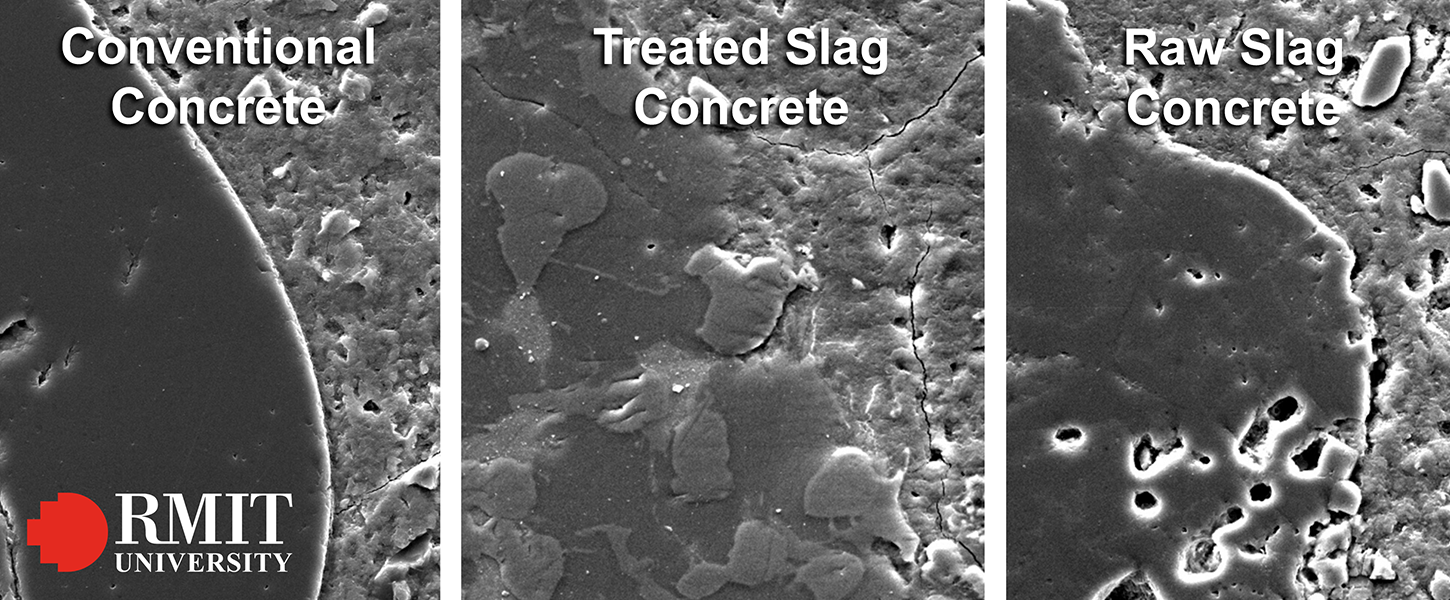
Blog 1: Double shot at circular economy - Steel slag soaks up toxins, then boosts concrete strength
Imagine a world where the by-products of steelmaking not only clean up wastewater but also contribute to creating stronger, more resilient concrete.
The Innovation
An inter-disciplinary research team at RMIT, jointly led by Dr. Rajeev Roychand (Civil) and Dr. Biplob Kumar Pramanik (Environmental), have cracked the code, revealing the power of steel slag in a zero-waste strategy that not only benefits the environment but also boosts the circular economy. This innovative approach not only removes harmful chemicals from municipal wastewater but transforms the chemical and mineralogical composition of the slag, making it a star performer in enhancing concrete strength. It's a double win for sustainability—cleaner water and stronger structures, all from a by-product of steel manufacturing process!
Transformation of Slag Chemistry after Water Treatment
The most dramatic change was the massive increase in iron content after filtration. XRF showed that iron oxides shot up from a mere 0.7% in the original slag to a whopping 30.5% post-sewage treatment. This iron was present in new crystalline compounds like calcium aluminum iron oxide and wuestite, which were completely absent in the raw slag. Interestingly, common slag minerals like akermanite-gehlenite were no longer detectable after wastewater filtration, likely transforming into amorphous phases. The sewage-soaked slag also formed new phosphate-containing crystals, suggesting that some of the phosphorus removed from the wastewater was chemically incorporated into the slag.
The Microscopic Detective Work
Scanning electron microscope images revealed densely packed crystalline compounds in the pores of the wastewater-treated slag. These compounds formed during the filtration process, strengthening the slag granules. Furthermore, both treated and raw slag chemically bonded better with cement compared to regular stone aggregates, creating a more cohesive microstructure.
The Green Dividend
Concrete made with the recycled slag aggregates achieved 32.5% higher 7-day strength and 8.2% higher 28-day strength compared to concrete made with untreated slag. The 28-day strength exceeded that of regular concrete by nearly 17%. The study shows how detailed knowledge of material chemistry can turn an industrial pollutant into a valuable resource, supporting the circular economy while making concrete production more sustainable.
Next Steps
While the initial results are promising, long-term durability studies are needed before this greener concrete can be used on a wider scale. Dr. Pramanik and colleagues are already planning these critical tests.
Research Team
Rajeev Roychand, Biplob Kumar Pramanik, Guomin Zhang, Sujeeva Setunge
Publication Reference
Recycling steel slag from municipal wastewater treatment plants into concrete applications – A step towards circular economy is published in the Journal of Resources, Conservation & Recycling (DOI: 10.1016/j.resconrec.2019.104533)
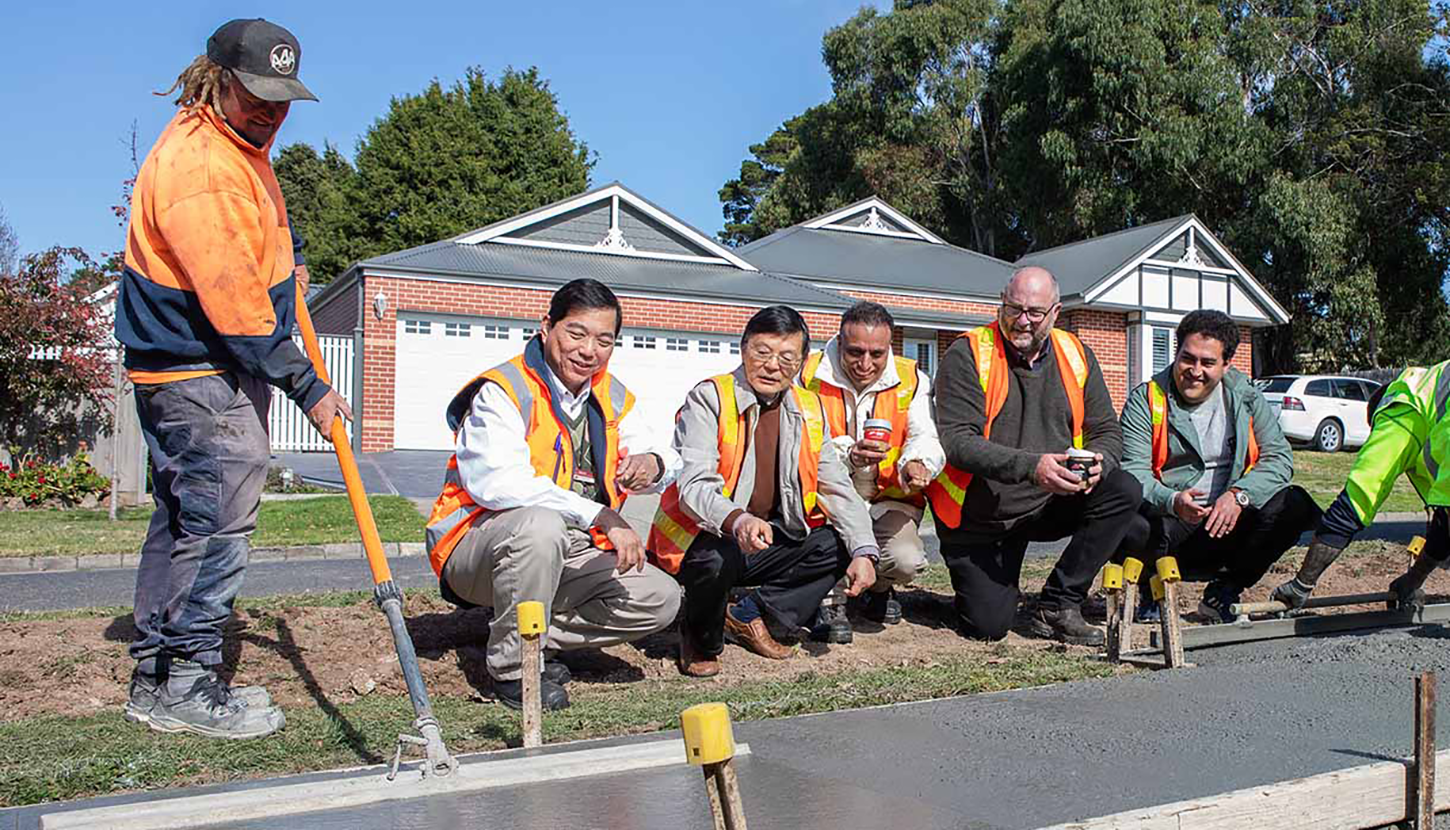
Picture Credit: Carelle Mulawa-Richards, RMIT University
From the Lab to the Sidewalk: The World's First Coffee Concrete Footpath
Last updated: May 23, 2024 06:30 PM AEST
In a groundbreaking collaboration between RMIT University and Macedon Ranges Shire Council, the world's first coffee concrete footpath has been laid, marking a significant milestone in the quest for sustainable construction practices. This innovative project builds upon the research conducted by Dr Rajeev Roychand and his team at RMIT, who discovered that transforming spent coffee grounds into biochar can dramatically enhance the strength of concrete while reducing waste sent to landfills.
The Power of Coffee Waste
Coffee is one of the most popular beverages worldwide, with millions of cups consumed daily. However, this popularity comes at an environmental cost. In Australia alone, approximately 75 million kilograms of ground coffee waste are generated annually, with the majority ending up in landfills. This figure skyrockets to a staggering 10 billion kilograms of spent coffee grounds each year. As the world becomes increasingly focused on sustainability and waste reduction, researchers have been seeking innovative ways to repurpose these waste materials and mitigate their environmental impact.
From Waste to Resource: The Coffee Biochar Process
The key to unlocking the potential of spent coffee grounds lies in a process called pyrolysis. By heating the grounds to a specific temperature (350°C) in the absence of oxygen, the RMIT researchers discovered that they could create a carbon-rich, porous material known as biochar. When incorporated into concrete at an optimal replacement level of 15% by volume of sand, this coffee-derived biochar increased the compressive strength of the concrete by an impressive ~30%. The porous nature of the biochar allows it to absorb water and contribute to the internal curing of the concrete, leading to enhanced strength development.
Putting Research into Practice: The Gisborne Footpath Trial
To put their research findings into practice, the RMIT team partnered with Macedon Ranges Shire Council to conduct a world-first coffee concrete footpath trial in Gisborne, Victoria. The trial involved incorporating coffee and wood-chip biochar into two separate concrete footpaths, replacing a portion of the river sand traditionally used in the mixture. Shane Walden, the Council's Director of Assets and Operations, expressed his excitement about the project, stating that residents won't notice any difference in the appearance or smell of the concrete, but the benefits to the environment and the community are significant.
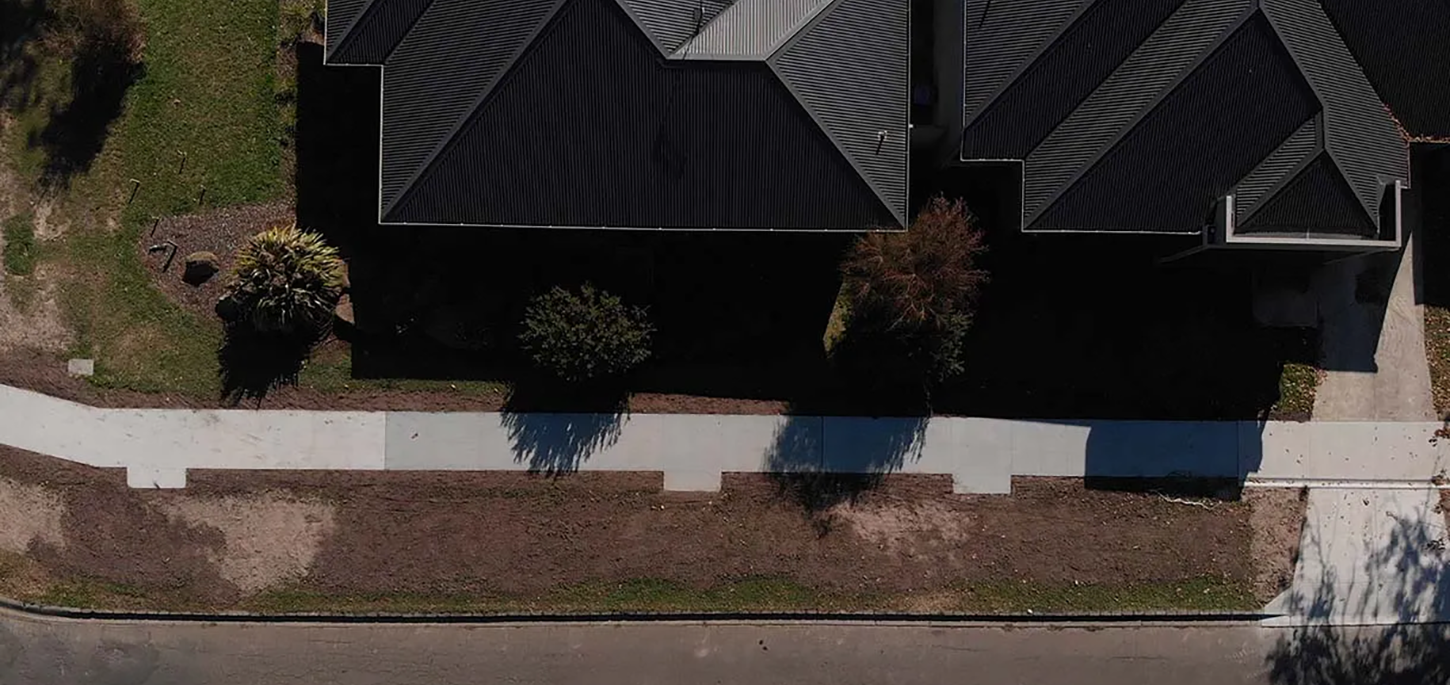
Aerial view of the finished footpath in Gisborne. Picture Credit: Chris Matthews, Macedon Ranges Shire Council
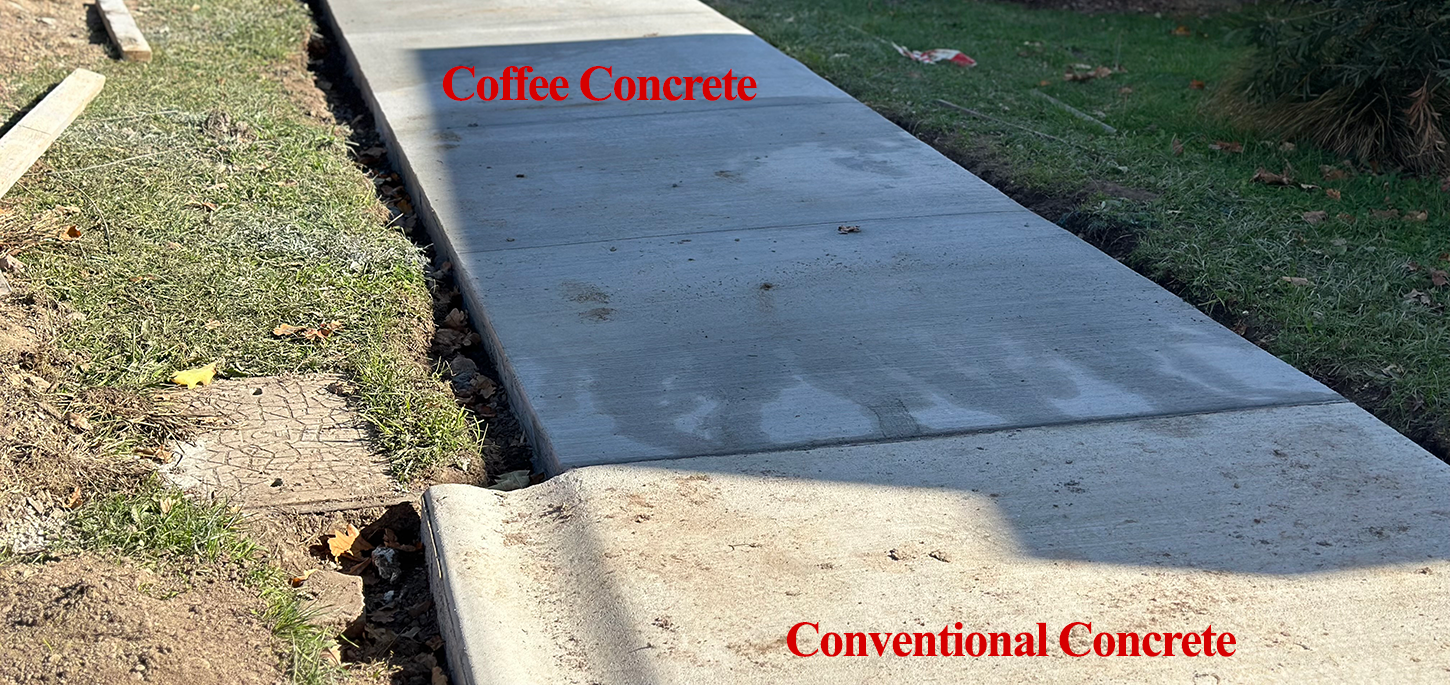
Close-up view of the finished footpath in Gisborne. Picture Credit: Jeetendra Kathayat, Macedon Ranges Shire Council
The Future of Coffee Concrete
Building upon the success of the Gisborne footpath trial, the RMIT team is now collaborating with BildGroup, an Australian-owned civil infrastructure, asphalt paving, and road profiling company, to deliver several upcoming coffee biochar concrete projects across Victoria. These projects aim to further validate the real-world performance and scalability of this innovative solution. By partnering with BildGroup, the researchers will have the opportunity to monitor the long-term durability and environmental benefits of coffee biochar concrete in various infrastructure applications. The collaboration between academia and industry is crucial in bridging the gap between laboratory research and practical implementation, paving the way for the wider adoption of sustainable construction practices. As more projects incorporating coffee biochar concrete are rolled out, the potential for this technology to revolutionize the construction industry and contribute to a greener future becomes increasingly evident.
Potential Benefits and Cost Savings
The incorporation of coffee biochar into concrete offers a range of potential benefits and cost savings for the construction industry. By achieving a 30% increase in concrete strength, the required cement content could potentially be reduced by as much as 10%, according to Dr Roychand. This reduction in cement usage, combined with the diversion of waste from landfills, promotes sustainability and supports the development of a circular economy.
List of Benefits
- Enhanced compressive strength: The addition of coffee biochar, particularly at a 15% replacement level of sand, can increase the compressive strength of concrete by up to ~30%.
- Potential for cement reduction: The significant increase in concrete strength due to coffee biochar incorporation could allow for a reduction in the required cement content, leading to lower environmental impact and cost savings.
- Waste utilization: By using spent coffee grounds to produce biochar for concrete applications, this waste material is diverted from landfills, promoting sustainability and a circular economy.
- Improved microstructure: Coffee biochar exhibits excellent bonding with the cement matrix, and the cement paste penetrates the porous biochar material, contributing to enhanced strength development.
- Internal curing: The porous nature of coffee biochar allows it to absorb and retain water, which is released as the internal relative humidity of the cement matrix drops, providing internal curing and further enhancing strength development.
- Reduced environmental impact: Incorporating coffee biochar in concrete can help reduce the carbon footprint of the construction industry by minimizing waste, reducing cement usage, and sequestering carbon within the concrete.
- Potential for large-scale application: The research suggests that 100% of the waste spent coffee grounds produced in Australia could be consumed by the construction industry if used as a replacement for fine aggregates in concrete.
- Improved sustainability: The use of coffee biochar in concrete aligns with the goals of sustainable construction practices and contributes to the development of eco-friendly building materials.
Research Team
Rajeev Roychand, Shannon Kilmartin-Lynch, Mohammad Saberian, Jie Li, Guomin Zhang, Chun Qing Li
Publication Reference
Transforming spent coffee grounds into a valuable resource for the enhancement of concrete strength is published in the Journal of Cleaner Production (DOI: 10.1016/j.jclepro.2023.138205)
Carbon sequestration from waste and carbon dioxide mineralisation in concrete – A stronger, sustainable and eco-friendly solution to support circular economy is published in the Journal of Construction and Building Materials (DOI: 10.1016/j.conbuildmat.2023.131221)
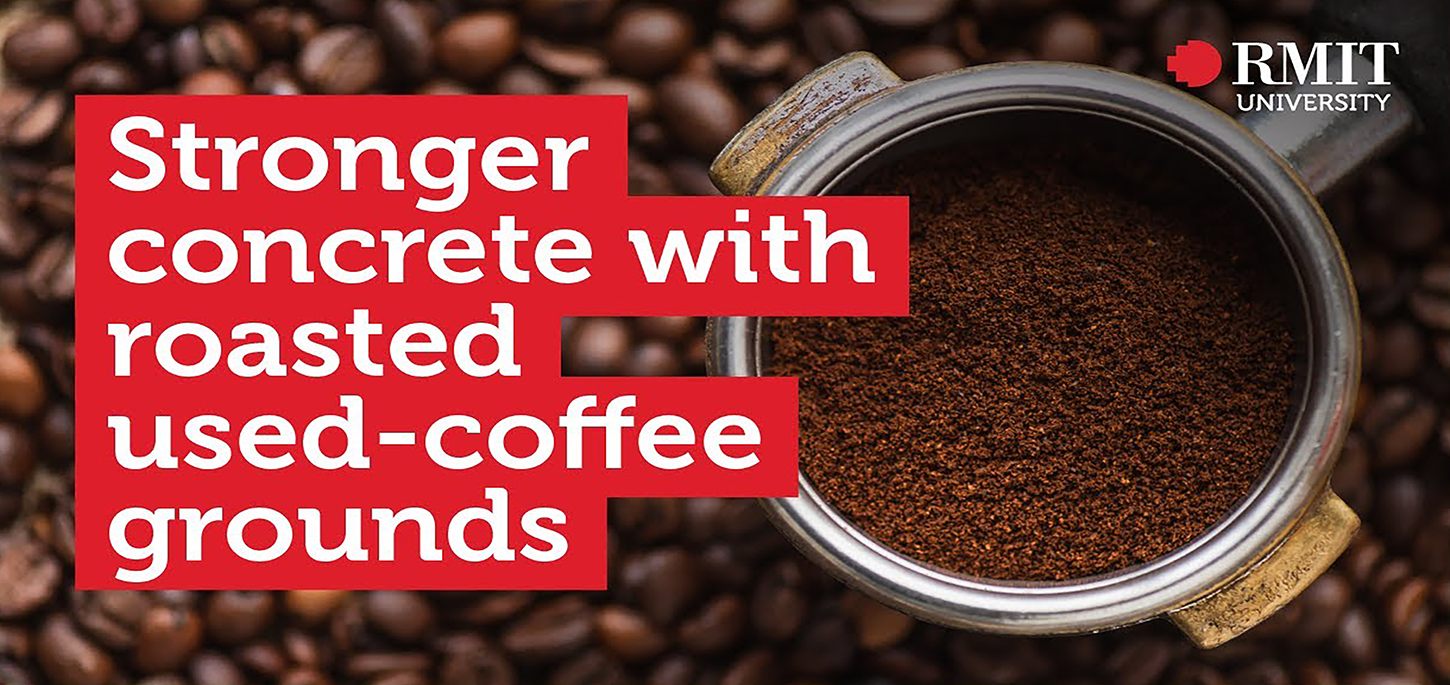
Picture Credit: RMIT University
From Lattes to Concrete: The Surprising Strength of Coffee Waste
Imagine sipping your morning latte and knowing that the spent coffee grounds from your cup could one day form the foundation of your home. This idea may soon become a reality, thanks to a groundbreaking study by engineers at RMIT University in Melbourne, Australia. They have discovered a way to create stronger concrete using roasted used coffee grounds, giving this popular beverage a second life as a building material while significantly reducing waste going to landfills.
Motivation Behind this Innovation
The driving force behind this groundbreaking study was the alarming amount of organic waste ending up in landfills, contributing significantly to greenhouse gas emissions. In Australia, approximately 6.87 million tonnes of organic waste are dumped in landfills annually, accounting for 3% of the country's total greenhouse gas emissions. Recognizing the urgent need to address this issue, the research team at RMIT University decided to shift their focus towards developing innovative solutions that could divert this waste from landfills and transform it into a valuable resource. Interestingly, the idea to start with coffee grounds emerged during a team meeting over a cup of coffee, highlighting the serendipitous nature of scientific discovery.
The Coffee Waste
Coffee is one of the most widely consumed beverages in the world, with millions of cups enjoyed daily. However, this popularity comes at a significant environmental cost. In Australia alone, around 75,000 tonnes of spent coffee grounds end up in landfills each year, contributing to a growing waste problem. Globally, this number skyrockets to a staggering 10 billion kilograms of coffee waste annually. As the world becomes increasingly focused on sustainability and waste reduction, researchers are constantly seeking innovative ways to repurpose these waste materials and mitigate their environmental impact.
From Coffee Waste to Biochar
Coffee is one of the most widely consumed beverages in the world, with millions of cups enjoyed daily. However, this popularity comes at a significant environmental cost. In Australia alone, around 75,000 tonnes of spent coffee grounds end up in landfills each year, contributing to a growing waste problem. Globally, this number skyrockets to a staggering 10 billion kilograms of coffee waste annually. As the world becomes increasingly focused on sustainability and waste reduction, researchers are constantly seeking innovative ways to repurpose these waste materials and mitigate their environmental impact.
Coffee Biochar for a Stronger Concrete
When incorporated into concrete, the coffee-derived biochar proved to have remarkable effects. At an optimal replacement level of 15% by volume of sand, the biochar increased the compressive strength of the concrete by an impressive 29.3%. The porous nature of the biochar allows it to absorb water and contribute to the internal curing of the concrete, leading to enhanced strength development.
The Role of Pyrolysis Temperature
The researchers found that the temperature at which the biochar is produced plays a crucial role in its effectiveness. Biochar created at 350°C provided the best results, while that produced at 500°C showed a decrease in strength due to its more fragile structure. This highlights the importance of fine-tuning the pyrolysis process to maximize the benefits of the biochar.
Environmental and Economic Benefits
- ~30% increase in concrete strength
- This significant increase in strength can be leveraged to reduce the required cement content
- Creates a potential for the 100% uptake of this waste material for concrete applications
- This waste to resource transformation creates a potential for diverting this waste from going to landfills, promoting sustainability, and closed loop circular economy.
Research Team
Rajeev Roychand, Shannon Kilmartin-Lynch, Mohammad Saberian, Jie Li, Guomin Zhang, Chun Qing Li
Publication Reference
Transforming spent coffee grounds into a valuable resource for the enhancement of concrete strength is published in the Journal of Cleaner Production (DOI: 10.1016/j.jclepro.2023.138205)
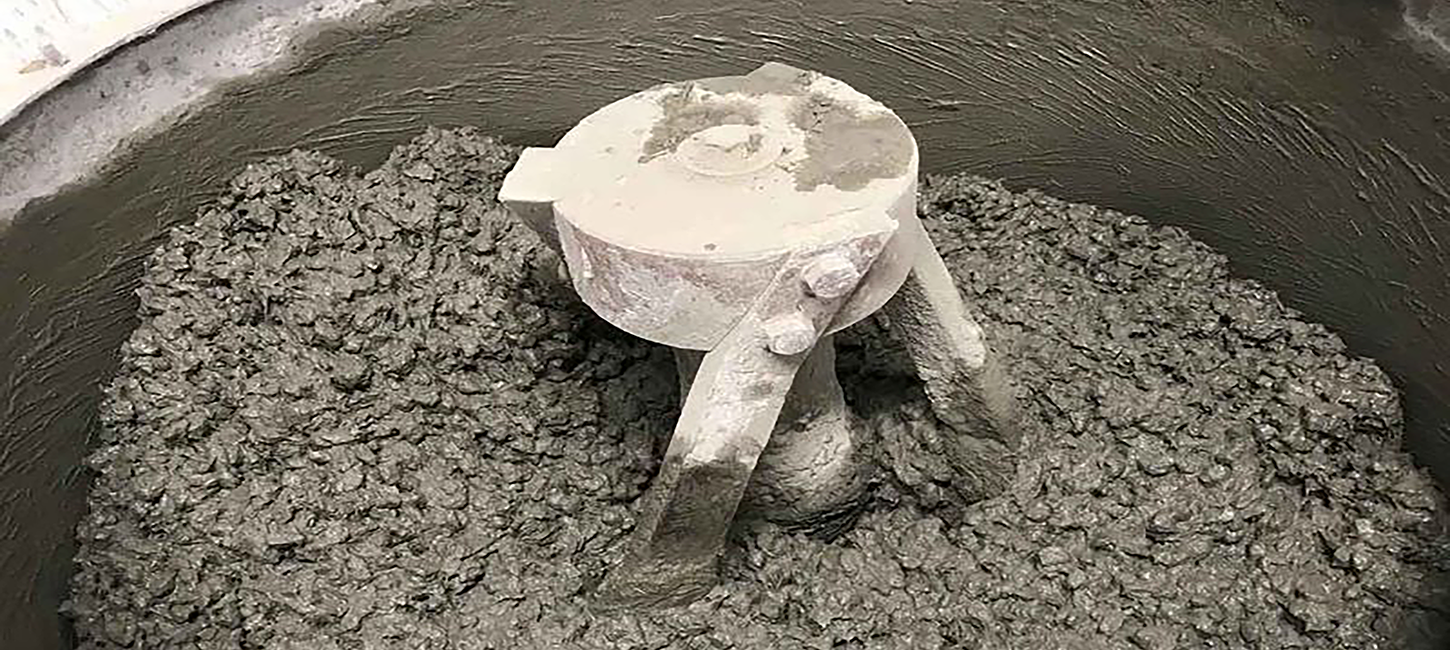
Picture Credit: Mohammad Islam, RMIT
Rubber Meets the Road: Transforming Tires into Sustainable Concrete
In a world where sustainability is no longer a choice but a necessity, engineers have achieved the remarkable feat of creating concrete that completely replaces conventional aggregates, such as gravel and crushed rock, with rubber derived from discarded tires.
A Pressing Issue
Every year, billions of waste tires end up in landfills, posing significant environmental challenges. These non-biodegradable materials not only occupy valuable land space but also contribute to air and water pollution when burned or stockpiled. The need for effective recycling methods has never been more urgent.
From Waste to Resource
Enter the visionary team of researchers from RMIT University in Melbourne, Australia. Led by Dr. Mohammad Momeen Ul Islam, they have developed an ingenious method that transforms waste tire rubber into a valuable resource for the construction industry.
Their innovative approach involves replacing conventional coarse aggregates in concrete entirely with rubber particles from end-of-life tires. By employing a novel compression casting technique, they have successfully created structural lightweight concrete with remarkable mechanical properties.
Strength and Sustainability
The rubber concrete developed by the RMIT team boasts a compressive strength of up to 97% higher than traditional rubberized concrete. This significant improvement in strength is achieved through the compression casting process, which minimizes the gaps between the rubber particles and the cement matrix, resulting in a denser and more durable material.
Moreover, the carbon footprint of this rubber concrete is substantially lower compared to conventional concrete. By utilizing waste tires, which would otherwise end up in landfills, the researchers have found a way to reduce the environmental impact of construction while also conserving natural resources.
A Greener Future
The potential applications of this rubber concrete are vast, ranging from residential construction to infrastructure projects. Its lightweight nature and impressive strength make it an attractive option for builders seeking sustainable alternatives to traditional concrete.
As the world grapples with the urgent need to combat climate change and reduce waste, innovations like rubber concrete offer a glimmer of hope. By turning waste into a valuable resource, we can pave the way to a greener, more sustainable future.
The research conducted by Dr. Islam, Dr. Li, and their team at RMIT University is a testament to the power of scientific ingenuity in addressing global challenges. As more industries embrace such eco-friendly solutions, we can look forward to a world where sustainability is not just a buzzword but a way of life.
Research Team
Mohammad Momeen Ul Islam, Jie Li, Yu-Fei Wu, Rajeev Roychand, Mohammad Saberian
Publication Reference
Design and strength optimization method for the production of structural lightweight concrete: An experimental investigation for the complete replacement of conventional coarse aggregates by waste rubber particles is published in the Journal of Resources, Conservation and Recycling (DOI: 10.1016/j.resconrec.2022.106390)
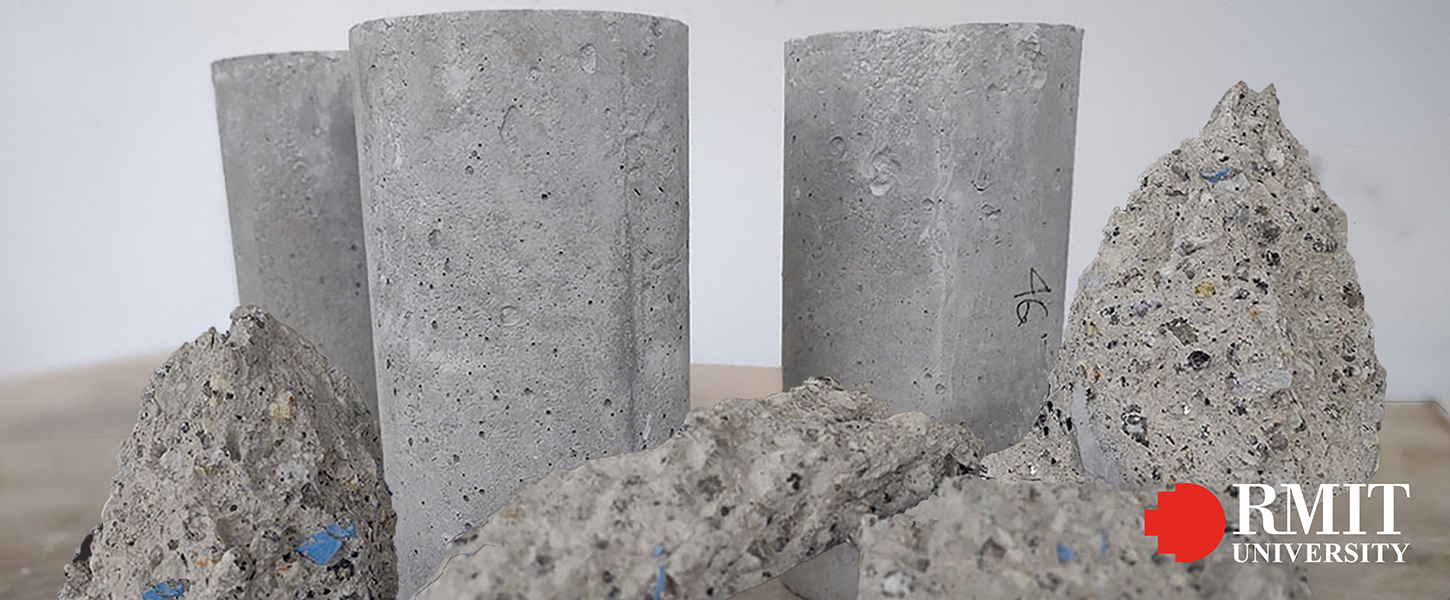
Picture Credit: RMIT University
Disposable PPE waste makes concrete stronger by up to 22%
Researchers at RMIT University have found a way to give new life to disposable personal protective equipment (PPE) waste by using it to strengthen concrete, offering a creative solution to the challenge of managing the surge of pandemic-related plastic waste. The RMIT team is the first to investigate the feasibility of recycling three key types of PPE – isolation gowns, face masks and rubber gloves – into concrete.
The environmental impact of PPE waste
The COVID-19 pandemic has not only strained healthcare systems worldwide but has also created a new stream of plastic waste in the form of discarded PPE. Globally, it is estimated that 129 billion face masks and 65 billion gloves are used each month. This surge in PPE waste has led to increased littering, with discarded items ending up in landfills and oceans, contributing to the growing problem of microplastic pollution.
Recycling PPE waste in concrete
To tackle this environmental challenge, the RMIT research team, led by Dr Shannon Kilmartin-Lynch, has investigated the potential of incorporating shredded PPE waste into structural concrete. By repurposing these materials, they aim to divert waste from landfills and reduce the environmental footprint of the construction industry.
- Nitrile gloves
- Polypropylene face masks
- Isolation gowns
Concrete Strengthening Mechanism
The researchers found that incorporating shredded PPE waste into concrete helps in improving its strength properties. The team attributed these improvements to the strong bond formed between the shredded PPE materials and the cement matrix, as observed through scanning electron microscopy. This strong bond allows for better stress transfer and crack bridging within the concrete mixture.
- Up to 22% higher strength with shredded nitrile gloves
- Up to 17% higher strength with shredded face masks
- Up to 15.5% higher strength with shredded Isolation gowns
Towards a circular economy
The research conducted by the RMIT team demonstrates the potential for a closed loop circular economy approach in the construction industry, where waste materials are repurposed as valuable resources. By incorporating PPE waste into concrete, not only can we reduce the environmental impact of the pandemic but also create a more sustainable built environment.
As the world continues to grapple with the challenges posed by COVID-19, it is crucial to find innovative solutions to manage the waste generated by the pandemic. The work of Dr. Li and his team at RMIT University serves as an inspiring example of how creative thinking and scientific research can help us build a more sustainable future.
Research Team
Shannon Kilmartin-Lynch, Rajeev Roychand, Mohammad Saberian, Jie Li, Guomin Zhang
Publication References
Application of COVID-19 single-use shredded nitrile gloves in structural concrete: Case study from Australia is published in the Journal of Science of The Total Environment (DOI: 10.1016/j.scitotenv.2021.151423)
Preliminary evaluation of the feasibility of using polypropylene fibres from COVID-19 single-use face masks to improve the mechanical properties of concrete is published in the Journal of Cleaner Production (DOI: 10.1016/j.jclepro.2021.126460)
A sustainable approach on the utilisation of COVID-19 plastic based isolation gowns in structural concrete is published in the Journal of Case Studies in Construction Materials (DOI: 10.1016/j.cscm.2022.e01408)
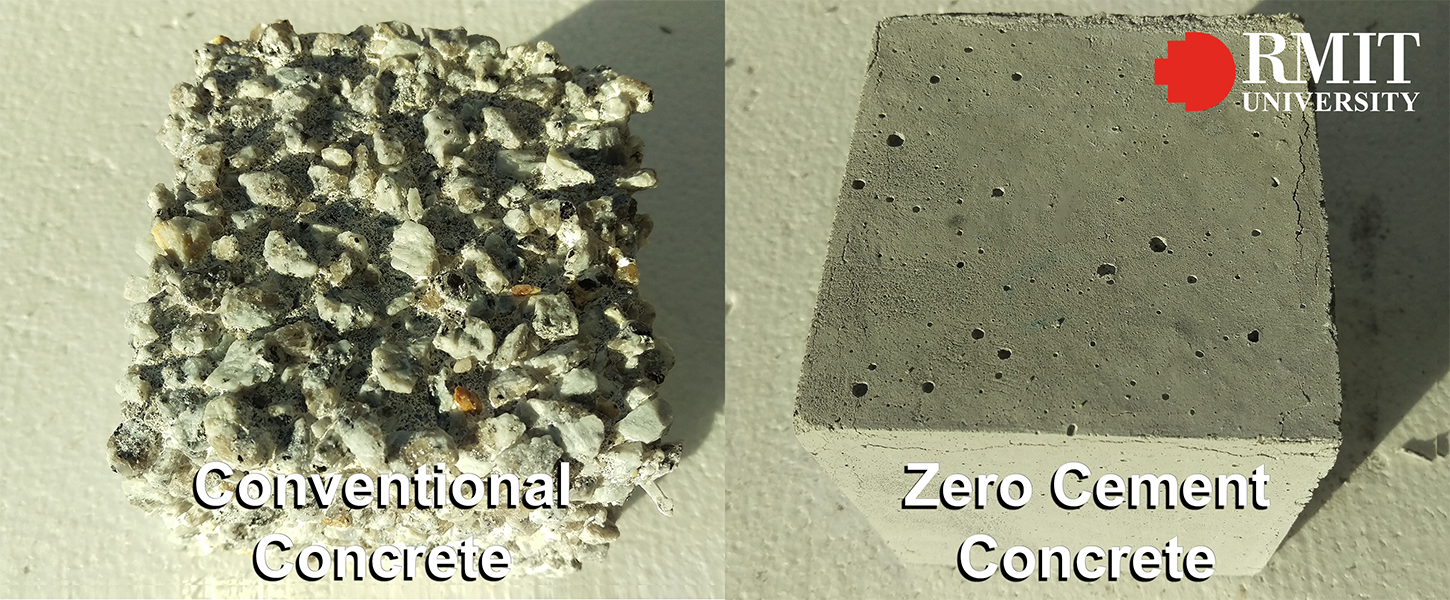
Picture Credit: RMIT University
High durability zero cement concrete beats corrosion and resists fatbergs
Researchers from RMIT University have pioneered an innovative zero cement concrete, wielding the power to eliminate corrosion and thwart the formation of fatbergs, thus extending the lifespan of infrastructure like never before.
The problem
Cement concrete, the backbone of our urban infrastructure, not only comes with high carbon footprint, but in the realm of sewage infrastructure, hides a dirty secret. The cement that binds the sand and gravel has a weak link i.e., free lime – a byproduct of cement hydration, that is released into the concrete. In the acidic sewage environment, the concrete rich in free lime becomes a vulnerable target to the corrosive acids, silently corroding the very core of sewage pipes. An even grimmer fate awaits on the inside of the pipes, where the same free lime reacts with fats, oils, and greases (FOGs) in the sewage to form giant, pipe-clogging "fatbergs". Maintaining and upgrading the sewage network comes with high costs and disruptions to the general public. With annual maintenance expenses reaching up to $15 million in Australia, tens of millions in the United Kingdom, and figure skyrocketing to billions in the USA, the financial burden on governments and taxpayers is undeniable.
Deciphering the Code
The team of researchers, led by Dr Rajeev Roychand, have cracked the code, unveiling how free lime, the hidden instigator of concrete corrosion, also plays a pivotal role in the formation of fatbergs. Furthermore, they have demonstrated how this innovative zero cement concrete, free from this inherent vulnerability, can play a crucial role in addressing these challenges.
The Innovation
By harnessing a cocktail of industrial byproducts like fly ash and slag, and fortifying it with nano-silica particles, the researchers have conjured up a concrete capable of withstanding the corrosive conditions inside sewers, while also help in preventing the sewers' worst enemies: corrosion and fatbergs. This innovation has the potential to revolutionize the way we build and maintain our infrastructure.
A sewer pipe dream come true?
While the researchers have shown it's possible to eliminate Portland cement from concrete sewage pipes, the long-term performance of this zero-cement concrete in real-world conditions still needs to be proven. Nevertheless, the study points the way to a future where concrete infrastructure is not only greener, but also lasts longer with less maintenance - a win for sustainability on multiple fronts.
Research Team
Rajeev Roychand, Jie Li, Saman De Silva, Mohammad Saberian, David Law, Biplob Kumar Pramanik
Publication Reference
Development of zero cement composite for the protection of concrete sewage pipes from corrosion and fatbergs is published in the Journal of Resources, Conservation & Recycling (DOI: 10.1016/j.resconrec.2020.105166)
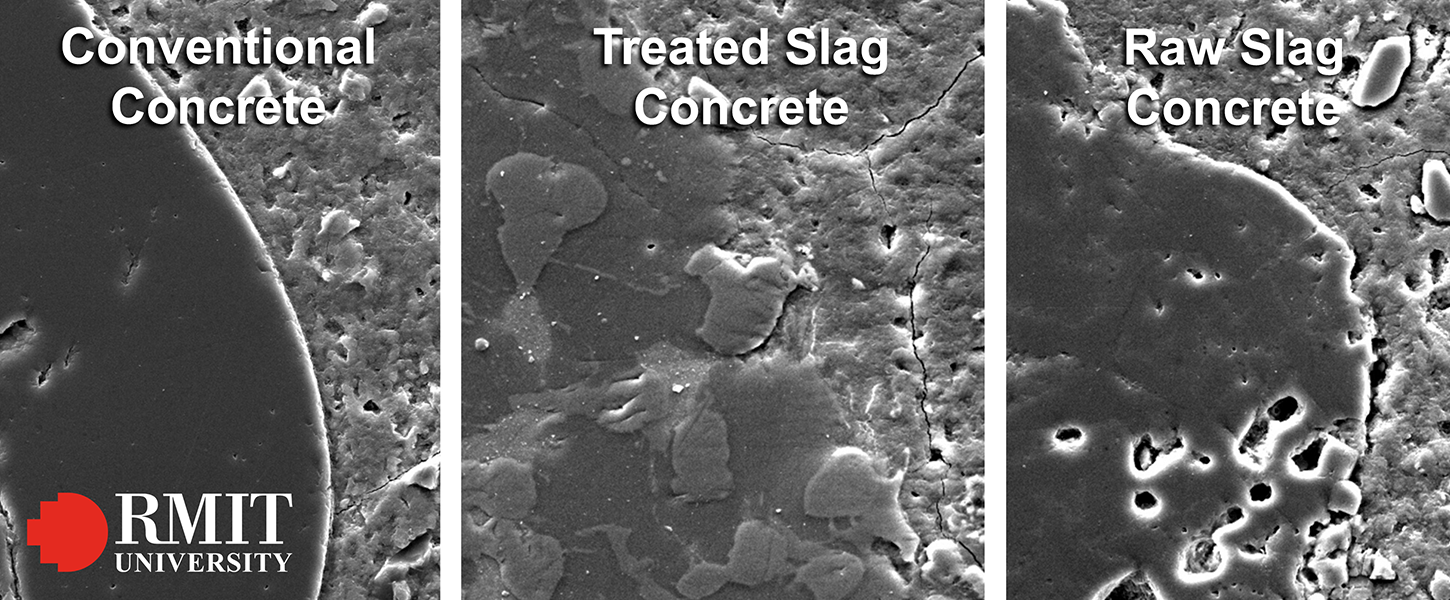
Picture Credit: RMIT University
Double shot at circular economy - Steel slag soaks up toxins, then boosts concrete strength
Imagine a world where the by-products of steelmaking not only clean up wastewater but also contribute to creating stronger, more resilient concrete. Steel slag is a by-product generated during the production of steel and is porous in nature. It forms when impurities in the raw materials used to make steel, such as iron ore, coke, and limestone, are melted and separated from the molten steel.
The Innovation
An inter-disciplinary research team at RMIT, jointly led by Dr. Rajeev Roychand (Civil) and Dr. Biplob Kumar Pramanik (Environmental), have cracked the code, revealing the power of steel slag in a zero-waste strategy that not only benefits the environment but also boosts the circular economy. This innovative approach not only removes harmful chemicals from municipal wastewater but transforms the chemical and mineralogical composition of the slag, making it a star performer in enhancing concrete strength. It's a double win for sustainability—cleaner water and stronger structures, all from a by-product of steel manufacturing process!
Transformation of Slag Chemistry after Water Treatment
The most dramatic change was the massive increase in iron content after filtration. XRF showed that iron oxides shot up from a mere 0.7% in the original slag to a whopping 30.5% post-sewage treatment. This iron was present in new crystalline compounds like calcium aluminum iron oxide and wuestite, which were completely absent in the raw slag. Interestingly, common slag minerals like akermanite-gehlenite were no longer detectable after wastewater filtration, likely transforming into amorphous phases. The sewage-soaked slag also formed new phosphate-containing crystals, suggesting that some of the phosphorus removed from the wastewater was chemically incorporated into the slag.
The Microscopic Detective Work
Scanning electron microscope images revealed densely packed crystalline compounds in the pores of the wastewater-treated slag. These compounds formed during the filtration process, strengthening the slag granules. Furthermore, both treated and raw slag chemically bonded better with cement compared to regular stone aggregates, creating a more cohesive microstructure.
The Green Dividend
Concrete made with the recycled slag aggregates achieved 32.5% higher 7-day strength and 8.2% higher 28-day strength compared to concrete made with untreated slag. The 28-day strength exceeded that of regular concrete by nearly 17%. The study shows how detailed knowledge of material chemistry can turn an industrial pollutant into a valuable resource, supporting the circular economy while making concrete production more sustainable.
Next Steps
While the initial results are promising, long-term durability studies are needed before this greener concrete can be used on a wider scale. Dr. Pramanik and colleagues are already planning these critical tests.
Research Team
Rajeev Roychand, Biplob Kumar Pramanik, Guomin Zhang, Sujeeva Setunge
Publication Reference
Recycling steel slag from municipal wastewater treatment plants into concrete applications – A step towards circular economy is published in the Journal of Resources, Conservation & Recycling (DOI: 10.1016/j.resconrec.2019.104533)